Choose the Right Materials
Every time we build a new house, do a renovation or demolish a building we release carbon to the atmosphere
But there are ways to reduce this Emissions from construction are known as embodied carbon footprint and come from the extraction, manufacturing, transportation, installation, maintenance, and disposal of building materials. Globally these make up 13% of all emissions.
Building materials may include reinforced concrete for your basement expansion, wood for a new deck, insulation for your low-energy retrofit or vinyl siding for your new garden suite. Choosing the right building materials can help us reduce this impact significantly.
Building materials may include reinforced concrete for your basement expansion, wood for a new deck, insulation for your low-energy retrofit or vinyl siding for your new garden suite. Choosing the right building materials can help us reduce this impact significantly.

You can explore our subsections on specific materials below:
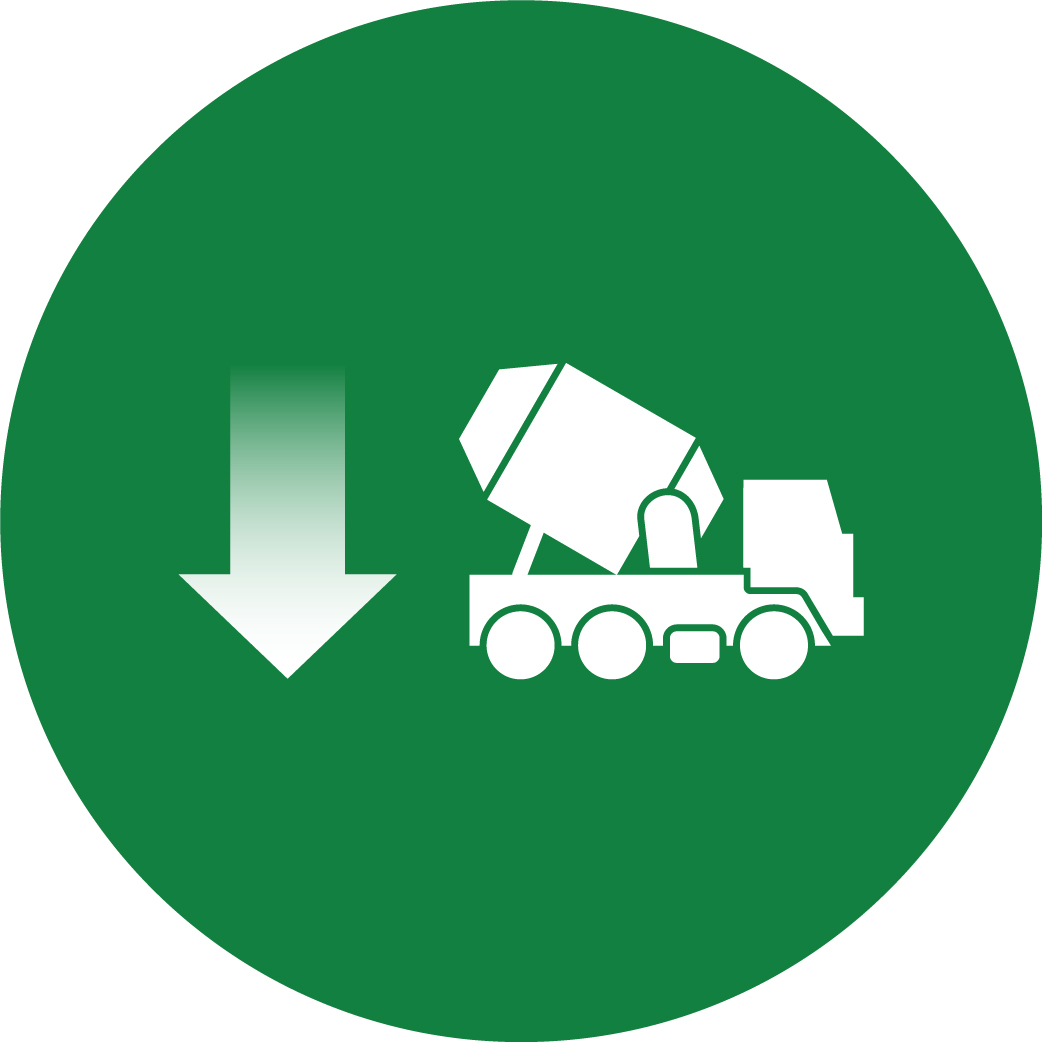
Reduce concrete

Low carbon insulation
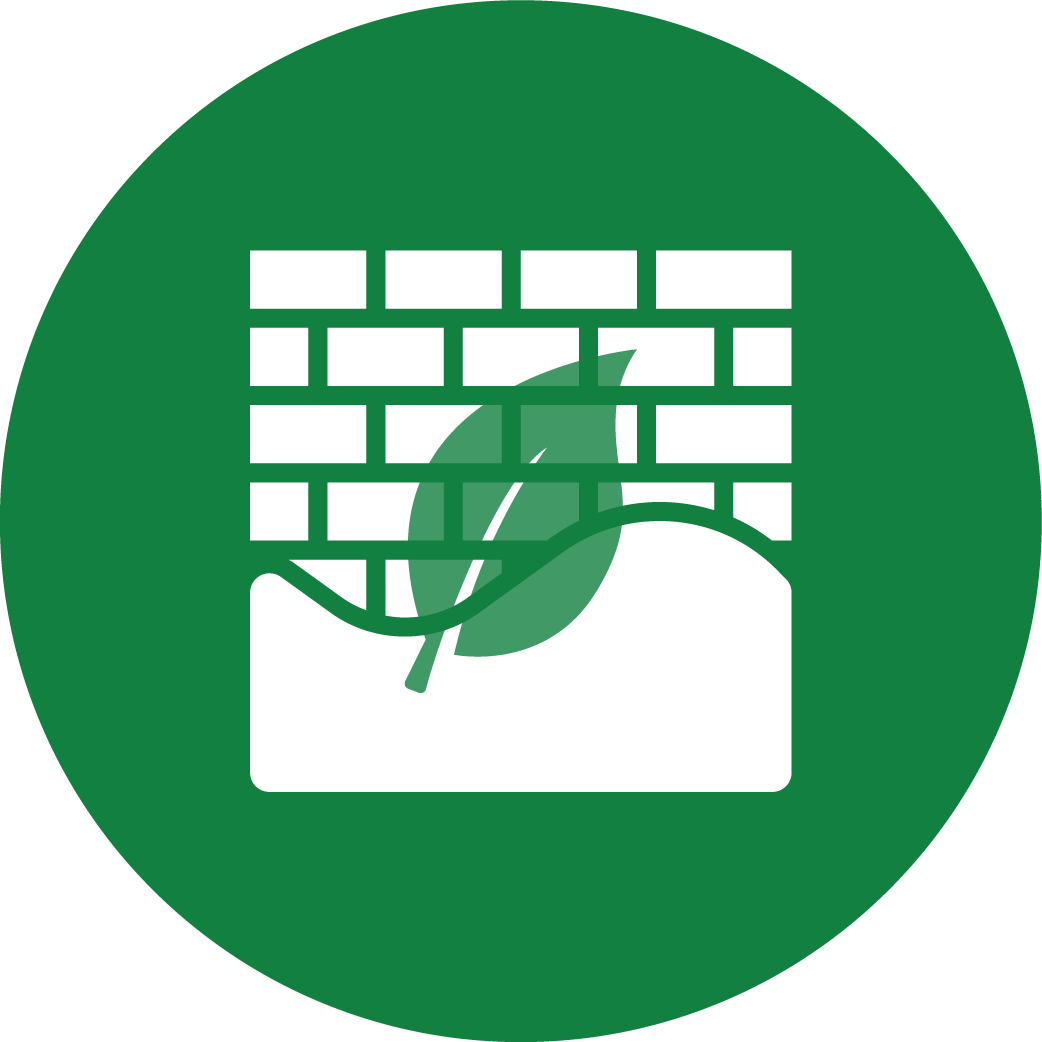
Biobased cladding
Is it affordable to choose building materials that reduce embodied carbon?
The market is flooded with options for building materials and very often you go with the cheapest option or with what your contractor suggests. But you can make material choices that will help reduce the carbon impact of your home without breaking the bank! The diagram below is from a 2021 Rocky Mountain Institute (RMI) report that shows significant reductions in embodied carbon footprint is achievable at low to no cost premiums.
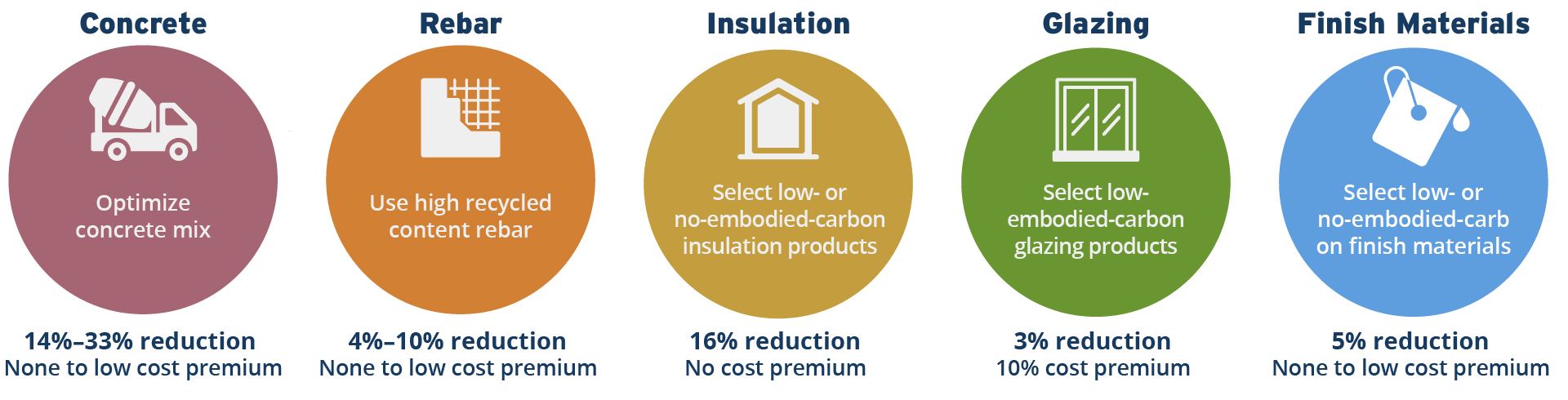
What are some general rules of thumb that can help you choose the right materials?
Reducing material quantity
The good news is that to lower the “embodied carbon” of your home does not necessarily mean higher costs. The most effective way to reduce the carbon footprint of materials is to build efficiently and use fewer materials. This can be done by taking a minimalist approach to structural additions and finishes - which also helps you to stay within your budget.
The good news is that to lower the “embodied carbon” of your home does not necessarily mean higher costs. The most effective way to reduce the carbon footprint of materials is to build efficiently and use fewer materials. This can be done by taking a minimalist approach to structural additions and finishes - which also helps you to stay within your budget.
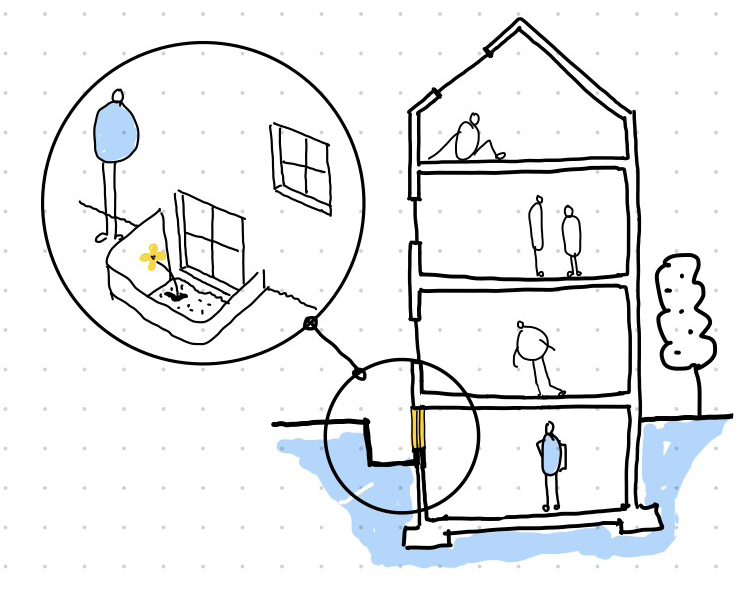
Use bio-based materials
This simply means using a material like wood wherever possible instead of concrete, steel and aluminium. Trees breathe in CO2 while they grow - so building materials made from wood have a negative carbon footprint in its raw material phase as opposed to the high levels of greenhouse gas emissions during the extraction of metals and petroleum based products like foam insulation. Other biobased materials include cellulose, hemp and straw bales which are locally produced, affordable and being used more commonly now in the GTHA.
This simply means using a material like wood wherever possible instead of concrete, steel and aluminium. Trees breathe in CO2 while they grow - so building materials made from wood have a negative carbon footprint in its raw material phase as opposed to the high levels of greenhouse gas emissions during the extraction of metals and petroleum based products like foam insulation. Other biobased materials include cellulose, hemp and straw bales which are locally produced, affordable and being used more commonly now in the GTHA.
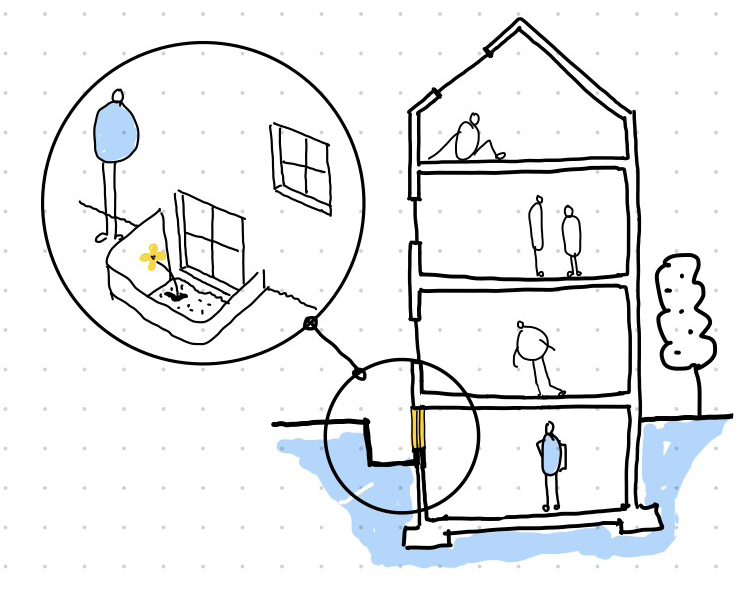
Choose lower carbon alternatives
Building materials now come with Environmental Product Declarations (EPD) which specify what its global warming potential (GWP) is. For example if you have to use foam insulation in your project EPS foam has a far lower carbon footprint than XPS foam - though they perform the similar functions and are priced the same. Ask your contractor for material EPDs with low GWPs. You don’t have to get into the nitty gritties of carbon accounting - but you can hold your General Contractor accountable for giving you the most environmentally viable options in your budget.
Building materials now come with Environmental Product Declarations (EPD) which specify what its global warming potential (GWP) is. For example if you have to use foam insulation in your project EPS foam has a far lower carbon footprint than XPS foam - though they perform the similar functions and are priced the same. Ask your contractor for material EPDs with low GWPs. You don’t have to get into the nitty gritties of carbon accounting - but you can hold your General Contractor accountable for giving you the most environmentally viable options in your budget.
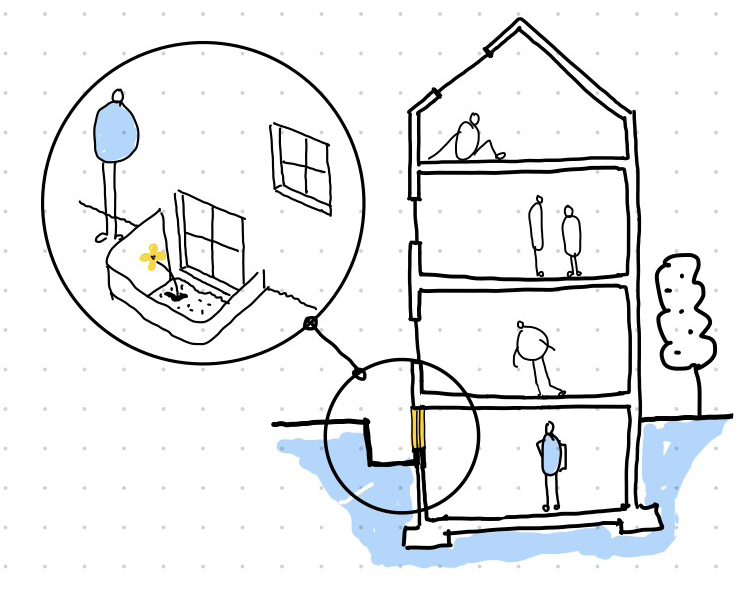
Reuse Materials
Whenever possible, try to salvage materials like brick, metals, broken concrete, or wood. Salvaged materials typically have a much lower embodied carbon footprint than newly manufactured materials, since the greenhouse gas emissions from their manufacture are already in the atmosphere. For example if bricks from a partition wall that is coming down during your home renovation can be repurposed as paving blocks of the path to your new garden suite - you save on both cost and carbon.
Whenever possible, try to salvage materials like brick, metals, broken concrete, or wood. Salvaged materials typically have a much lower embodied carbon footprint than newly manufactured materials, since the greenhouse gas emissions from their manufacture are already in the atmosphere. For example if bricks from a partition wall that is coming down during your home renovation can be repurposed as paving blocks of the path to your new garden suite - you save on both cost and carbon.
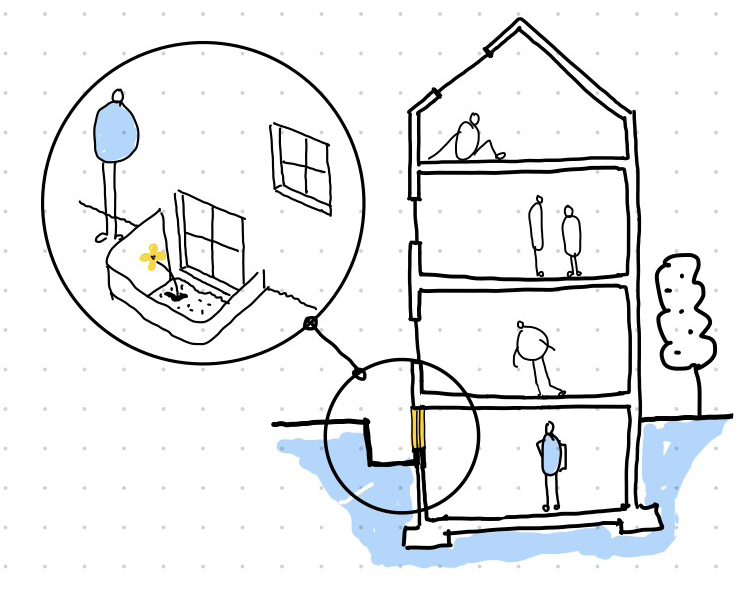
Consider material durability and end of life options
It makes obvious sense to choose materials with a longer lifespan from both a cost and carbon saving point of view but this should be judged against the above considerations. But sometimes a material that lasts longer can actually have a negative environmental impact once the building is no longer in use or needs to be replaced. For example spray foam insulation can last 100 years but is often used in buildings that are upgraded or replaced every 30 years- and needs to be landfilled. Instead cellulose insulation will last 20-30 years and after this substantial use-life it will naturally biodegrade rather than become a permanent problem in the waste stream.
It makes obvious sense to choose materials with a longer lifespan from both a cost and carbon saving point of view but this should be judged against the above considerations. But sometimes a material that lasts longer can actually have a negative environmental impact once the building is no longer in use or needs to be replaced. For example spray foam insulation can last 100 years but is often used in buildings that are upgraded or replaced every 30 years- and needs to be landfilled. Instead cellulose insulation will last 20-30 years and after this substantial use-life it will naturally biodegrade rather than become a permanent problem in the waste stream.
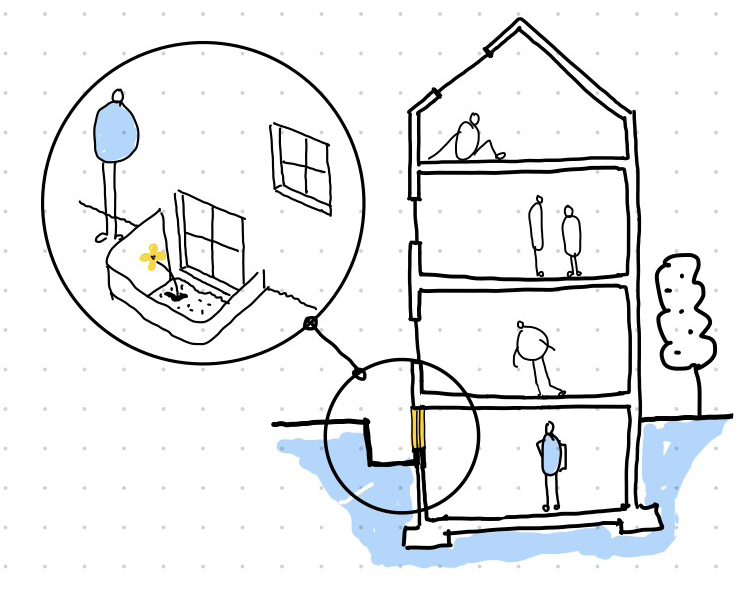
Recent studies show that in low rise residential construction in the GTHA , three major building material categories are responsible for 72% of embodied carbon emissions.
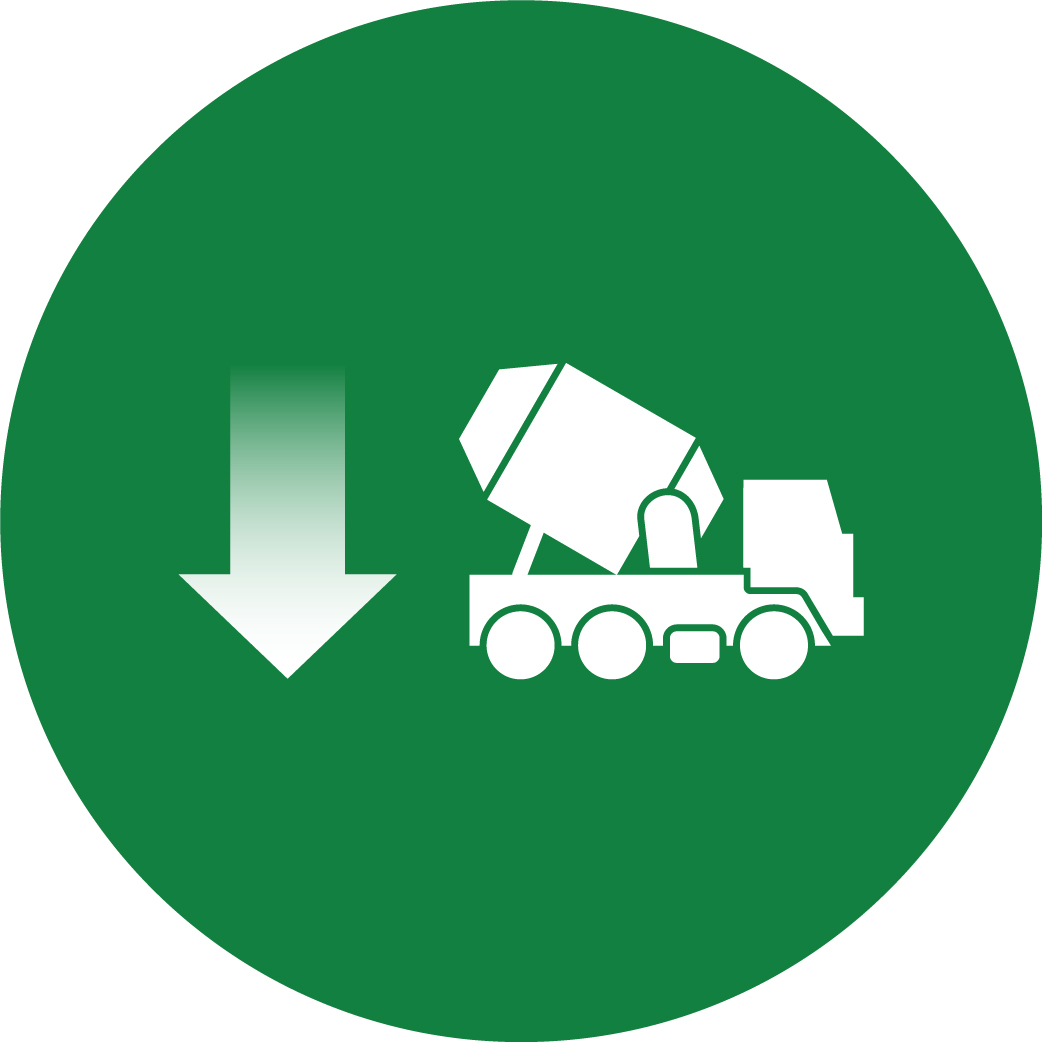
Reduce concrete use
1. Concrete Elements
Concrete Elements that make up foundation walls, slabs, footings, basement construction and underground parking comprise 33% of total embodied emissions.

Use low carbon insulation
2. Insulation Products
Insulation products are part of exterior wall, roof and floor assemblies and include rigid board, semi rigid batt and loose fill that are typically made from petrochemicals. These make up 26% of total embodied emissions.
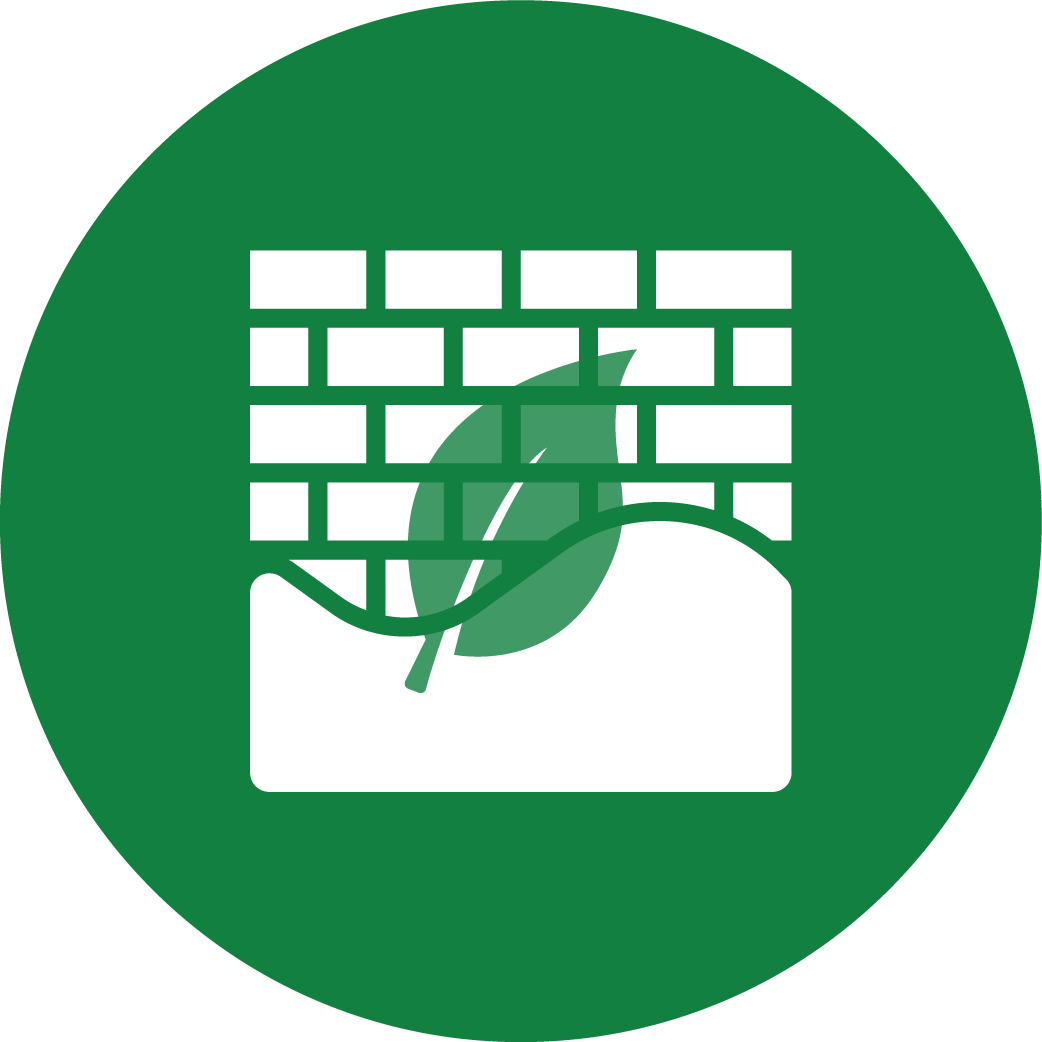
Select bio-based cladding
3. Exterior Cladding
Exterior cladding are materials that is used to finish the building's facade and is typically brick, vinyl, aluminium or fibre cement all of which have very high embodied emissions and add up to 13% of the total.